Join devRant
Do all the things like
++ or -- rants, post your own rants, comment on others' rants and build your customized dev avatar
Sign Up
Pipeless API
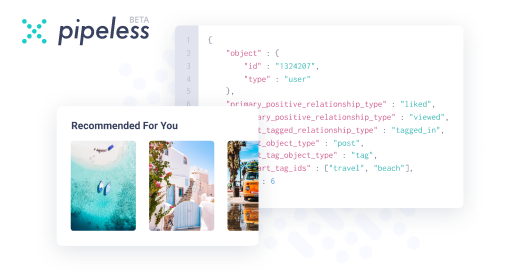
From the creators of devRant, Pipeless lets you power real-time personalized recommendations and activity feeds using a simple API
Learn More
Related Rants
So I just received this second DSP5005 DC-DC programmable power supply. Time to make an enclosure for the thing!! 3 power supplies totaling at around 1kW, and 2 variables connected to the 50V 10A one, through external banana wires (I want all of this to be modular). No biggie, take measurements for the AC-DC supplies, add in the variables on the front, and cut it out.
So, I went and did just that. Now my 500W (50V 10A) supply is a bit larger than the others, and it's got a fan. So I figured, well then probably my 24V 8.3A (200W) and 12V 15A (180W) supplies could use some cooling as well. But how am I going to achieve passive cooling without a spacing between the supplies?! So I thought of some spacer design. It had to be out of wood, and I had some 4mm MDF and some IKEA parts around. So, 4mm MDF for the plate and 8mm wood spacers from IKEA for the spacing. And some super glue to hold it all together.
Weighing my power supplies against a 1l bottle of milk, it seems like my power supplies are ~500g. Great, so the top spacer would take 500g and the bottom one 1kg + the weight of the top spacer.
I ended up building one plate with 6 spacers in it yesterday, until I got too tired. Then I placed my entire weight against it, 20kg at least. It didn't budge. Pretty good for something that's only designed to withstand a 1kg load!!
So, I made something good with only a 10x18cm piece of MDF, some garbage from IKEA, and most importantly a bit of a brain. Something that can handle 20x its designed load no problem. Manufacturers, is it really right to produce shit when I can beat your manufacturing processes big time without an assembly line?!
rant
diy
electronics
build it yourself
certified enganeers