Ranter
Join devRant
Do all the things like
++ or -- rants, post your own rants, comment on others' rants and build your customized dev avatar
Sign Up
Pipeless API
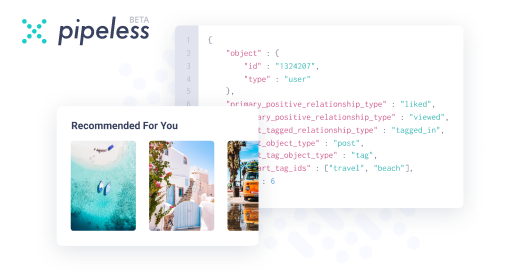
From the creators of devRant, Pipeless lets you power real-time personalized recommendations and activity feeds using a simple API
Learn More
Comments
-
// https://andyhemingway.files.wordpress.com/...
calling_the_herd(Hardware)
{
User[ ] = { @Alice, @Condor , @nightowl , @7400 , @LuxARTS , @Crowns , @mngr , @JoshBent, @BadCompany , @shellbug , @c3ypt1c, @devTea , @rEaL-jAsE , @sbiewald , @Gregozor2121 , @Haxk20 , @Cozyplanes , @S-Homles-MD , @ewpraten , @ganjaman , @MisterArie , @No-Flux-Given , }
}
// If you want to me removed or changed to other category leave a reply -
If you can post pictures of that beautiful creation i would at least be able to know what im dealing with.
-
@Mizz141
Rest in pepperonis...
Ok coming back to the topic:
30W is small in comparison to other soldering irons. Everything depends how much time you spend heating up the legs, what temp are you using and how good your joints are.
PS. Are you powering them up correctly? Also you can damage them only it you mess around the IC, not the board. -
@Gregozor2121 I know they are working because I have been using one for a bot. Because I was using ISP to program one of the pins fell, so I had to resolder... And ended up resoldering more pins. What W you recommend to solder electronic components?
-
LuxARTS15957yI don't think the heat was the problem. The flux thing it's not possible. The best way to find what's going on is checking with a multimeter.
-
Burning parts with solder is not so easy.
I think you made a shortcut somewhere throw them away and next time do a continuity check before powering them -
Can you point me to a tutorial where I can learn how to do continuous checks please? Thank you
-
Gonna buy a soldering station. What temperature should I use to soldier electronic stuff btw?
-
Condor315657yGet a better soldering iron, 30W isn't going to maintain a stable temperature. 60 or 75W (preferably station) should work fine. Then you can just put it on 450°C or so and melt through the joints like butter.
-
Condor315657y@GyroGearloose The brand velleman doesn't give me very good memories (one of their hubs lasted me for years before it got somehow drenched into soap, but that's about it) so I probably wouldn't buy it because of that.. but yeah, the specs don't seem too bad. Especially if it's (edit: it's, not tit's.. :/) temperature-controllable.
-
Would still like that link or tutorial for continuity check guys.
Found some continuity check tutorials but not for arduino (watching the others anyway) -
Sooo... good thing, both nanos work again, but not on the circuit I had build...
And can't find any wire out of place... -
Yep, All this crap and it's some bug in the circuit that I can't find.
Maby I fried the L293D?
At least didn't lose the Nanos...
And ordered 5 more
And finally bought a good soldering station. -
Condor315657y@GyroGearloose Continuity check is essentially measuring a resistance between 2 points in your circuit that are usually below 1 ohm. Continuity is essentially the obverse of resistance, so a conductive trace is continuous while one of those continuous points to something completely different in the circuit is going to be gapped by a strong insulator. The insulator's ability to resist voltage arcs is also commonly referred to as the dielectric strength, which is a measure of the amounts of MV it takes for a meter thickness of an insulative material to strike an arc right through it.
-
@Condor So... guide me trough...
I'm testing the Nano with a multimeter.
Should I select Ohms? And how much? Or the buzzer?
Witch pins should I check? -
Condor315657y@GyroGearloose I'd look online for the expected voltages on each pin (VCC should be 5V, ground should be 0V, your designated signal pins should have their appropriate voltages etc etc) as well as the values of the most common components.. also check for shitstains on the board. If something's fucked, it'll likely be noticeable by the component being deformed, having either an open circuit or short, etc etc. Troubleshooting is an art of its own, so it takes the ability to follow clues and make hypotheses, then prove or disprove them to get to your endpoint - the fucked component. In case of the Nano however, I'd just say - buy a new one. Most of the components there are SMD which are pretty difficult to replace.. and Nano boards are pretty cheap anyway.
-
Well, the problem wasn't the soldering, not the L293D or the batteries...
Redone everything and used a Uno this time.
Works flawlessly.
I'm gonna create a post for my second bot now with pictures -
A 30W soldering iron? For electronics?! That's crazy. Get a 15W with pointed tip. I'm using this one: https://eve-electronics.com/ersa-li...
You can of course use a soldering station with much more power if it's temperature controlled, but that's more expensive.
Flux in itself doesn't conduct, but can lead to long term corrosion damage, so better remove that afterwards. Also, I recommend leaded tin-solder with flux inside.
Do you have a solder sucker for removing excess tin or unsoldering unwanted connections? -
@ganjaman Really not bad, arround double from China, Thanks for the robotdyn tip
-
@Fast-Nop I do have an electric solder sucker was using it half an hour ago to salvage an old board.
Thought that more whats were better... Well already got the station, but the cheapest soldering iron for electronics (15W) was more expensive. And I really like this soldering station, already fucked up another older model that my dad had. And I still have it here to exchange the iron.
how do you remove the flux afterwards? is there a good practical way? -
@GyroGearloose more watts are only better if you need to heat up more metal, like for rain pipes. Or big cables, but you shouldn't solder those anyway. If you have a soldering station, you just need a fine, pointed tip (really important!) and set the temperature to what your tin-solder requires. Unleaded needs more temp than leaded.
I remove the flux with my fingernails. If my dick were as hard as my fingernails, I'd be a porn star instead, so that works. And for the finer spots, I use a plastic toothpick. -
@Fast-Nop So, what temperature would you recommend? I can't say if my solder is leaded or not...
-
@GyroGearloose the package should say if there is lead in it, look for "Pb" - the chemical designation for lead. Leaded tin melts at around 200°C, unleaded at 230°C or so. The tip has to be hotter than that since it cools down when heating up the tin. Typical ballpark is melting temperature + 100°C.
In my ex-company, we had at lot of leaded tin for maintenance things, and suddenly the safety people came around and declared that as dangerous substance that had to be disposed of properly. Luckily, we had gotten warning and had opted for "decentralised disposal"(tm). -
@CozyPlanes they aren't bad for prototyping, or for giving non-embedded folks a low entry barrier, like model railway enthusiasts or art projects.
For actual embedded, you can get much cooler boards like Olimex H405. Cortex M4 with 1 MB ROM, 192 kB RAM and a whopping 168 MHz. -
Condor315657y@Fast-Nop I'd say that more watts are better because it allows the iron to heat up faster (less waiting, more better) and ensures thermal stability better, especially when you're dumping a lot of heat into a big joint (like power rails, with fat rails, close by heatsinks etc) and are using a thin curved conical tip for increased precision. In a 15W iron I kinda doubt that there'll be thermal stability of any kind when it's put into (or rather, onto) a fat joint.. so I wouldn't like to work with that. But maybe it'd be useful for in the field, when you couple it with some batteries 🤔
For removing flux I use isopropanol. You can put some on a cotton swab and give the board some rubbing with it. Or for particularly nasty places, maybe a toothbrush but I found that it doesn't hold onto the isopropanol very well. You can find isopropanol at the pharmacist by the way.. I don't know about others but my local pharmacist sells it at €1.50/100ml in little plastic bottles. -
@Condor soldering electronics doesn't have big heat sinks, and if you're heating up a lot of tin, you're probably doing it wrong.
Yeah big power rails and stuff, but that's stuff where soldering is bad anyway because that stuff has to be crimped and not soldered. After all, bad crimping would heat up and weld, giving good contact again. Bad soldering would dis-solder, giving a light arc, dropping liquid metal and generating sparks, that's why.
For electronics tinkering, a 15W iron is perfectly fine, I'm doing that myself this way for private stuff.
Of course, a temperature controlled soldering station with lots of power if needed is the luxury solution that combines the best of both worlds, that's what I have at work. -
Condor315657y@Fast-Nop mostly heatsinks as in other components where the heat may escape to as well.. think IC's etc which need to be cooled back down afterwards. They only reach probably around 60°C whenever I worry about those things (hot but not all that unsafe to touch) so I don't think it's a problem.. and none of them die so that's always a good thing. But 15W isn't a whole lot of thermal energy.. hence my concern. And there's good soldering stations for just €40 nowadays anyway, which I would say is a no-brainer when compared to all the issues that my previous irons had.
As for mechanical connections (crimping, screw terminals, etc) I generally try to avoid that, as solder connections are more stable, don't displace after a bit of a tug and so on.. at the cost of reduced serviceability though.
As for bad crimping vs bad soldering, both should be caught and taken care of by QC in commercial products, no? Or in the DIY stuff, it should just be redone. Keeping the wire from dancing around during consolidation of the joint is imperative. Usually I just hold it with my hand during through-hole soldering (tweezers damage the plastic I've found.. and silicone wire can get pricey) and hold it or tape it down when doing surface-mount lines. That way, good joints can be easily made 🙂 -
@Condor well for soldering stuff like ICs, sprit board points, resistors and whatnot, I've never un into a problem with my 15W iron. However, the heat has to actually be put into the tip, and I guess bad soldering irons just heat up anything beside the tip. ERSA is a well-known brand here, so I don't have that issue.
40 EUR for a whole station - I'd instead go for the iron alone, but that's a matter of taste I guess. I prefer lower tech at higher price if in doubt.
As for the mechanical things, electric soldering joints are not meant to bear mechanical stress. If that's the case, the construction itself is wrong. That's just for quick & dirty botch when I'm too lazy even for hot glue and lighter. -
Condor315657y@Fast-Nop well the station that I'm using here is a T12 compatible.. so the temperature sensing components, heating element etc are all contained into the tip with no mechanical heat transfer being required (that's why I prefer T12 or similar ones where the tip goes all the way into the handle, as opposed to ones where the tip is just that, and screwed in or similar). Slightly more expensive, but really worth it.
As for my station.. €40 has always impressed me for this 75W station.. I think that it may be a loss leader. Either way, I quite like it! That thing is truly a joy to work with.
Regarding the mechanical stress.. of course it isn't supposed to be an expected thing, just like it isn't expected that people pull power cords out of the wall by pulling on the wire instead of on the plug. But just in case, I would definitely want the wire to have some resilience against tugs, especially when it's carrying high voltage. Safety is a big concern for me, as I haven't insured my property (apartment is, but my goods aren't). So having something shit the bed and burn my house down would be devastating. Hence why I'm so worried about that in my own designs, and check for it when I open up store-bought stuff for inspection. The case, screws and things like that are the first line of protection, but the power lines themselves definitely need it too. That's where good solder joints come in. -
Btw the soldering station I got was €36.
I bought this one because my dad already had the same (older version) and I really liked it until I fucked the tip.
This version has a fast nob to exchange the tip and metal placeholder.
The cheapest pen soldering Iron was €45 for a 15W and €60 for a 25W. (ERSAs)
I guess when I get more experience I can even change the temperature to adjust for different components.
Repeating helps a lot.
I'll rebuild a shield I did that was fucked up by the big 60W Iron (It's 60W, not 30W). to test stepper motors.
And probably make a shield for the car when I decide what I'll place on top of it (Trying to decide between my 10 toy guns which would be better... And Also the camera. I'll use one of the Arduinos with build in Wifi for the camera. -
I'm getting good at this... And the station helped a lot.
So. Used maximum heat (tried at 300 C, took time to melt, tried at around 450 C and it worked perfectly.
Soldered my third nano in less than 5 minutes.
Almost perfect cones.
no bridges.
Trying to do continuity test by myself now... Lets see if it works right -
@CozyPlanes you don't even have to. Arduino is using C++, but they have a framework that takes care of the boilerplate and low level stuff so that you can just enter your own code, which is called a "sketch".
And here is the kicker, the Arduino community has sketches for nearly everything. It's this ecosystem that makes Arduino fly. The usual workflow is googling for a sketch that does what you need, copy/paste, then compile and download. Done. -
@CozyPlanes You don't really need to know C.
The language is so basic that you learn the basics in the first tutorials.
Everything is always the same.
For Ifs and switch cases you just need to know any language, Ifs, Switches, Fors are the same in all languages.
You can even build the entire projects only with Variables and some IFs. -
@Fast-Nop @GyroGearloose (whispers) Let's just say I only love C# and Microsoft. Ssshhhhh
Hey guys
I think I just burned 2 Nanos.
I'm using a 30W soldering Iron and had to resolder the pins of one and solder the pins of a new one.
Now they don't work. One allows for code upload but won't turn on, other seams to have a short circuit.
Could have I burned the circuits due to a 30W soldering iron?
Also used a little of flux on the pins, can flux pass energy and make bridges?
Thanks
rant
fucked my nanos
arduino nano